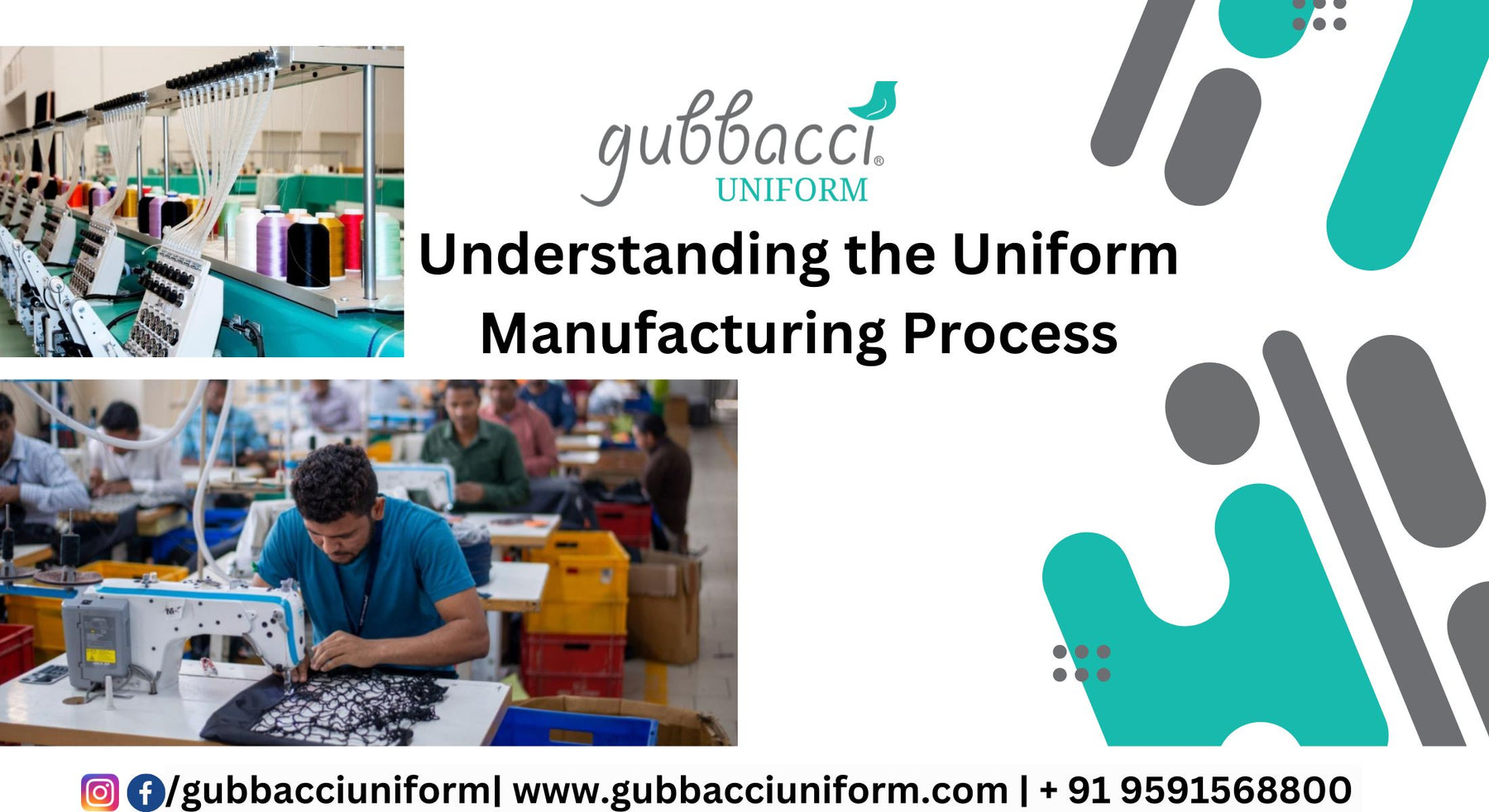
Understanding the Uniform Manufacturing Process
Have you ever wondered what goes into creating the uniforms we wear every day, whether for work, school, or sports? The process of manufacturing uniforms is a interesting blend of creativity, precision, and efficiency. From selecting the right fabric to cutting, stitching, and quality check, every step is crucial to ensure a perfect fit and long-lasting durability.
From Design to Delivery: The Uniform Manufacturing Process
There are several steps in the uniform manufacturing process, all of which are essential to ensure that the finished product satisfies customer requirements, maintain quality standards, and is delivered on schedule. Below is a detailed overview of the entire uniform production, from the initial design phase to the final delivery of uniforms.
Design Phase
- In the initial discussions with the client, fabric options(such as cotton or polyester), design preferences (e.g. style, fit, or colour), and customizations (logos or embroidery) are covered.
- After the specifications are discussed, using digital tools, the uniform design team creates samples and sketches.Custom elements, such as embroidery or screen-printed logos, are incorporated into the design.
- The client reviews and provides feedback. Once approved, the design moves on to the production stage.
Material Sourcing and Testing
- The uniform manufacturer purchases necessary raw materials, including labels, buttons, zippers, threads, and textiles. Requirements for appearance, comfort, and durability must be met by suppliers.
- Certain manufacturers maintain inventory of standard materials, while others place custom fabric orders based on client demands.
- Fabrics are examined for colour stability, durability, breathability, and shrink resistance upon arrival to make sure they satisfy quality control and industry requirements.
Pattern Making and Cutting
- Based on the agreed design, patterns are made for each piece of clothing, specifying how the fabric should be cut so it has the proper size and shape, such as the cuffs, collars, and sleeves.
- The fabric is then carefully put out, frequently in big rolls, and then cut into the necessary forms. Skilled workers can complete this task by hand, or for accuracy and efficiency, automated cutting machines can be used.
Sewing and Assembly
- The sewing section receives and assembles the cut pieces. This involves stitching hems, zippers, side seams, cuffs, collars, and sleeves.
- Adding reinforcement to areas like elbows or knees (if needed for industrial uniforms) are also done at this stage.
- The garment is regularly inspected for quality at this point. Any issues such as incorrect stitching, uneven seams, or misplaced components are identified and corrected before proceeding to the next step.
Customization and Finishing
- Embroidery machines create durable, professional logos or names on fabric, while screen printing is ideal for larger or complex designs, applying ink for branding on garments.
- Adding features like glowing strips or stronger stitching, or placing buttons and labels, are examples of final touches.
- Uniforms are then pressed or ironed for a polished finish, using industrial presses or hand irons as needed.
Quality Control and Inspection
- Every uniform is examined for defects such as improper sizes, fabric errors, stitching problems, and irregularities in the print or embroidery.
- Each garment is thoroughly inspected by the team to make sure it satisfies both the client's and the supplier's specifications.
- Items are returned to the appropriate department (such as sewing or customisation) for repairs if problems are found.
- The clothes undergo a second round of quality inspections after the required repairs are completed before being cleared for shipping.
Packaging and Labeling
- The uniforms are packaged after passing inspection. This may consist of hanging uniforms on display racks, folding them, or bagging them.
- Each garment is labeled with essential information such as size, fabric content, care instructions, and branding details (e.g., company logos).
- Labels for larger orders could have barcodes or batch numbers to help with inventory management.
Delivery and Distribution
- Shipment of the finished uniforms to the customer completes the procedure. Standard or expedited delivery may be used by the manufacturer, depending on the quantity of the purchase and its urgency.
- The uniform manufacturer may follow up with the customer again after delivery to make sure they are satisfied with their purchase.
- Any problems with fit, sizing, or personalization can be fixed, and if necessary, more orders or modifications can be placed.
Gubbacci Uniforms specializes in offering quality, personalized uniforms for companies, MBA programs and schools. We are committed to maintaining industry standards and prioritize customer interaction to deliver college and school uniforms that meet specific requirements. We ensure accuracy, comfort, and an elegant look for each uniform from design to delivery. Reach out to us today to experience superior quality and tailored service for all your uniform needs.
Leave a comment